What is Porosity in Welding: Finest Practices for Avoiding Porous Welds
What is Porosity in Welding: Finest Practices for Avoiding Porous Welds
Blog Article
Porosity in Welding: Identifying Common Issues and Implementing Ideal Practices for Prevention
Porosity in welding is a prevalent issue that typically goes undetected up until it causes significant troubles with the integrity of welds. This common defect can compromise the strength and durability of welded structures, posturing safety and security threats and resulting in pricey rework. By understanding the root causes of porosity and carrying out efficient prevention methods, welders can considerably improve the top quality and integrity of their welds. In this discussion, we will explore the essential aspects adding to porosity formation, analyze its damaging results on weld performance, and discuss the very best methods that can be taken on to decrease porosity event in welding procedures.
Usual Root Causes Of Porosity
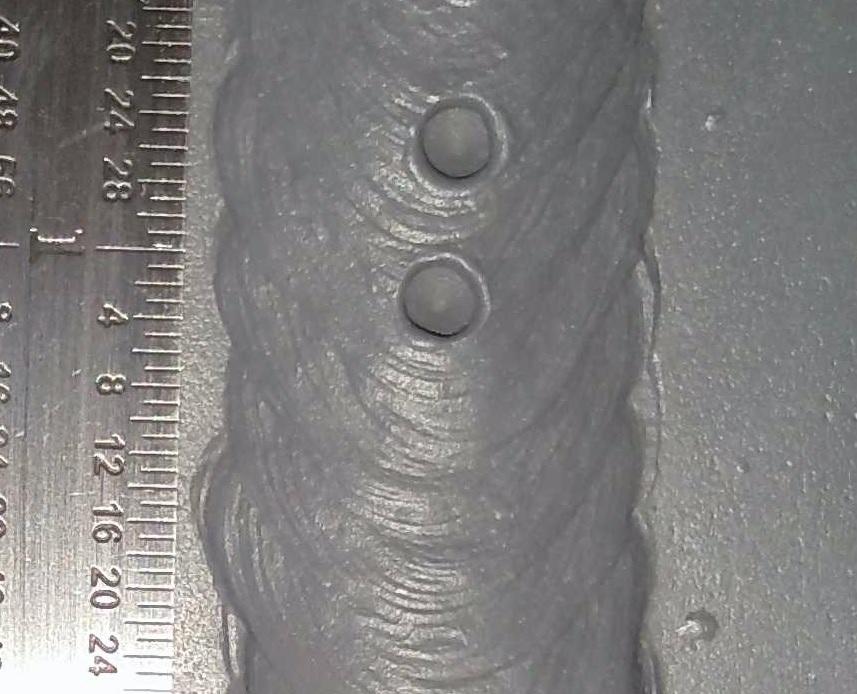
Using unclean or wet filler materials can introduce impurities right into the weld, contributing to porosity issues. To minimize these usual reasons of porosity, thorough cleansing of base metals, proper protecting gas selection, and adherence to ideal welding criteria are vital methods in achieving top notch, porosity-free welds.
Effect of Porosity on Weld Top Quality

The existence of porosity in welding can significantly endanger the structural stability and mechanical properties of bonded joints. Porosity creates spaces within the weld steel, weakening its overall toughness and load-bearing capability.
Among the key effects of porosity is a decrease in the weld's ductility and toughness. Welds with high porosity degrees often tend to show reduced influence toughness and lowered capability to flaw plastically prior to fracturing. This can be specifically worrying in applications where the welded components are subjected to dynamic or cyclic loading conditions. Porosity can hinder the weld's capacity to properly transfer forces, leading to early weld failure and possible security dangers in critical frameworks. What is Porosity.
Ideal Practices for Porosity Avoidance
To boost the structural stability and quality of bonded joints, what certain measures can be executed to decrease the incident of porosity during the welding procedure? Porosity avoidance in welding is important to ensure the honesty and strength of the last weld. One reliable method appertains cleaning of the base steel, eliminating any kind of contaminants such as rust, oil, paint, or wetness that could cause gas entrapment. Making certain that the welding devices is in great condition, with tidy consumables and appropriate gas circulation prices, can likewise substantially reduce porosity. Furthermore, maintaining a stable arc and managing the welding criteria, such as voltage, present, and take a trip rate, helps develop a consistent weld swimming pool that decreases the risk Get More Info of gas entrapment. Utilizing the correct welding strategy for the particular material being welded, such as adjusting the welding angle and weapon position, can better protect against porosity. Routine evaluation of welds and immediate remediation of any kind of issues identified throughout the welding procedure are crucial practices to protect against porosity and generate top quality welds.
Importance of Appropriate Welding Strategies
Carrying out proper welding methods is extremely important in making sure the structural stability and top quality of bonded joints, building upon the structure of reliable porosity avoidance actions. Too much warm can lead to raised porosity due to the entrapment of gases in the weld swimming pool. Furthermore, making use of the proper welding parameters, such as voltage, current, and travel rate, is vital for attaining sound welds with minimal porosity.
Moreover, the option of welding procedure, whether it be MIG, TIG, or stick welding, should line up with the certain needs of the project to make sure ideal results. Correct cleaning and preparation of the base steel, along with choosing the appropriate filler product, are likewise necessary parts of proficient welding methods. By adhering to these look at here now finest practices, welders can decrease the risk of porosity development and produce high-quality, structurally sound welds.
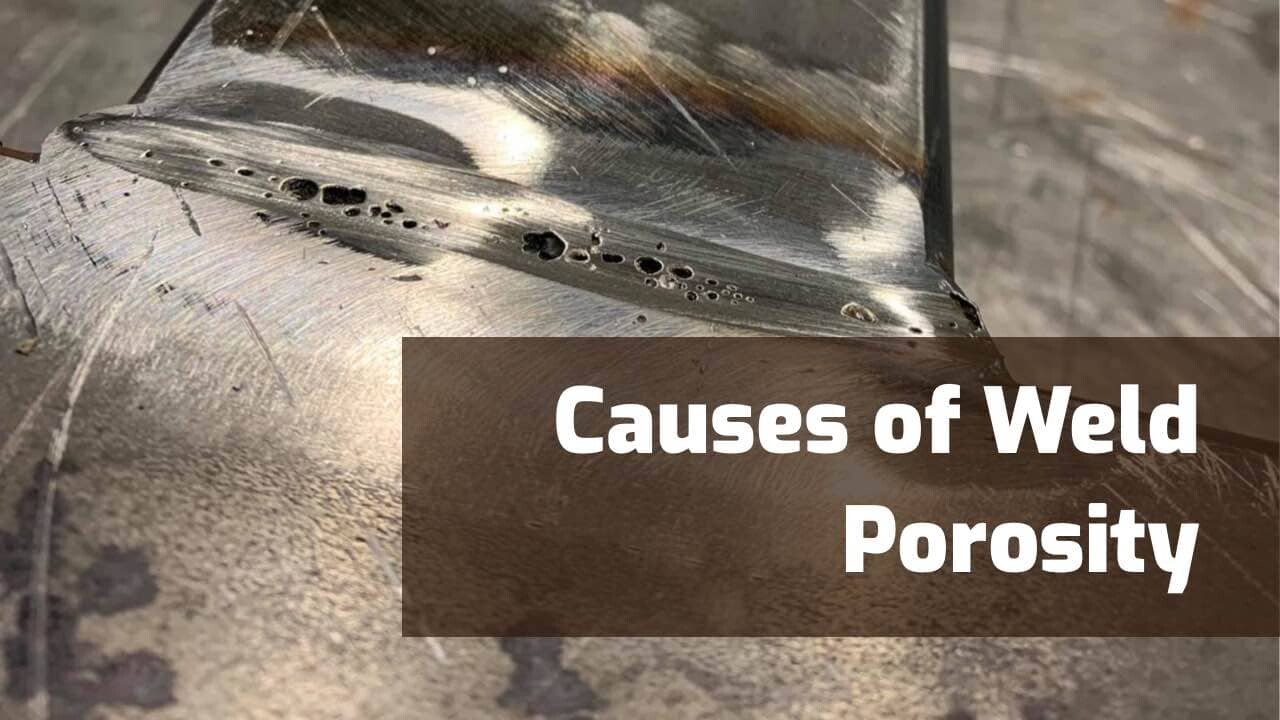
Testing and Quality Control Procedures
Testing procedures are important to spot and avoid porosity in welding, ensuring the toughness and sturdiness of the last product. Non-destructive testing techniques such as ultrasonic testing, radiographic testing, and visual evaluation are generally employed to determine possible flaws like porosity.
Post-weld inspections, on the other hand, assess the final weld for any type of flaws, consisting of porosity, and verify that it satisfies defined criteria. Implementing a thorough top quality control plan that consists of comprehensive screening treatments and evaluations is vital to lowering porosity problems and ensuring the general quality of welded joints.
Conclusion
Finally, porosity in welding directory can be a typical concern that affects the top quality of welds. By identifying the typical sources of porosity and carrying out best techniques for prevention, such as proper welding methods and testing steps, welders can ensure premium quality and reliable welds. It is vital to prioritize avoidance methods to reduce the event of porosity and preserve the stability of welded frameworks.
Report this page